GMV GSharp®
Safe High-Accuracy Reliable Positioning Solution
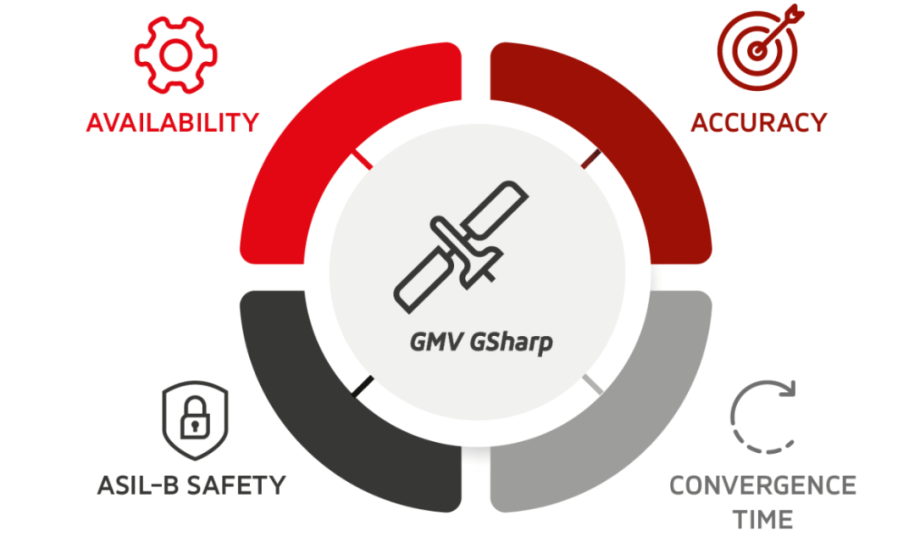
Proprietary solution for multiple GNSS domains
- Solution conceived to cover multiple end user applications, from the ones solely seeking high accuracy GNSS products, to the ones aiming for safety critical applications.
- Proprietary Global Positioning Solution that enables GNSS users to determine their position or trajectory with highest accuracy.
- Both Safe Correction Service and Safe Positioning Engine are fully developed and maintained by GMV and inherit more than 30 years of experience in GNSS.
Our engineering support team is not only there to assist you, but to gather your insights with the aim of move our service closer to the users’ needs.
- Our engineering team has not only developed and validated our solution but is part of the on-call engineering support team, increasing the technical responsiveness of our customers’ requests or issues.
- GMV’s solution is always evolving based on our customers’ needs; from tailored GNSS products for specific scientific applications, on-demand performance and analysis reports, to the implementation and support of new real-time corrections formats.
- Highlight that our engineering support is one of the most valued assets from our solution based on our customers’ feedback. This brings a great deal of satisfaction to our team, as 100% of our customers have renewed their service over the past years.
Our commitment to our customers is to provide the highest possible reliability for our solution, both in terms of performances and availability. Real-time monitoring is key for ensuring the best reliability figures and provide a prompt reaction.
- The Safe Correction Service (SCS) includes a monitoring layer which provides status, data in timeseries and statistics for the CORS status, GNSS corrections computation, safety processor integrity computation and delivery of corrections data to the delivery chain. The selections done at each epoch between the redundant chains and load-balancing elements is also monitored.
- Security is becoming a critical driver for most of the services and applications. In this regard a continuous security monitoring of the Safe Correction Service (SCS) infrastructure is done. The monitoring is performed by GMV’s computer emergency response team (CERT) service which is a certified implementation of Carnegie Melon CERT.
- All logs of the system and sensitive elements are permanently monitored and hazardous events are reviewed. In case any relevant event is identified a dedicated process to handle it is launched. Additionally, periodical black and whitebox pentest are conducted in the system.
Best end user performances can only be achieved by being able of performing an accurate GNSS product estimation. GMV has deep knowledge of the different GNSS constellations thanks to over 30 years of experience on precise GNSS orbit determination.
- GMV’s deep involvement in the Galileo Programme has driven the need to excel in exploiting the constellations’ capabilities in terms of orbit accuracy.
- Being the only private company who is a real-time IGS analysis centre, puts GMV’s Solution in the spotlight when benchmarking all GNSS’ constellations performances against renown GNSS-related institutions such as ESOC, DLR, CNES, among others.
- The SPE has been put to the test under the harshest conditions, not only by our engineering team, but by our customers too. Constant SPE improvements to maximize end user performances are engraved within our DNA.
Safe Correction Service (SCS), element in charge of calculating the satellite orbits, clocks, biases, and ionospheric corrections together with the associated integrity flags and error bounds.
- Service provides flexibility based on customers’ needs in terms of correction rates, constellations, formats, or safety aspects. Access to the service is selected by the customers (NTRIP Caster, Apache Kafka, MQTT,…).
- Two redundant processing facilities are operated and monitored in a 24x7 regime, at US and EU, in dedicated HW (not shared/virtualize on cloud services). These HW is hosted in TIER-3/TIER-3+ Data Centres, ensuring the highest availability levels.
- The processing facilities provide standard high accuracy corrections and safe high accuracy corrections, covering different user needs. For safe correction service, a safety processor system developed following ISO26262 and ISO21448 validates the corrections and provides additional integrity information.
Safe Positioning Engine (SPE), on-board element which processes the GNSS information provided by the measurement engine, in combination with the IMU data, other sensors and the corrections service data. It provides position, velocity, track angle, heading angle and the associated integrity status and protection levels for the different outputs.
- The PE implements a set of safety monitors validating all the input data and discarding measurements or information which could compromise the integrity of the processing.
- The PE has been developed following the ISO26262 for ASIL-B process, and ISO21448 (SOTIF) process. Additionally, a security process has been followed to evaluate the risks doing a security concept and TARA to derive the necessary security and cyber security requirements.
- Provides accurate and reliable output based on the processing of GNSS raw measurements and corrections, hybridizing with IMU data, odometer information and wheel speed sensors, when available.
- Deep SW optimisation for lightweight processing, successfully migrated to multiple user platforms, easing integration processes.
Global GNSS Station Network (GGSN), worldwide reference network deployed, owned, and operated by GMV. Continuous monitoring of all flying GNSS satellites from no less than 4 reference stations at any time. Data measurements are sent at 1 Hz both in RTCM and binary formats to GMV’s operation centres, where it is processed and analysed in real-time, prior to its distribution to external or internal users.
- The CORS configuration comprises 40 triply redundant multi-GNSS reference stations. Four of the reference stations’ receivers are driven by atomic frequency standards, providing a redundant source for stable timing reference.
- Data from CORS are archived both for post-processing applications and off-line performance analysis during a minimum period of 1 month with direct-access (i.e. SFTP/cloud service) and lifetime with slow access (i.e. requested on-demand to operations team).
- All stations are equipped with independent security layers, including anti-tampering. Measures have been implemented within each station to enable the usage of data for safety critical applications.
GMV GSharp® for LEO missions provides precise file based GNSS products with minimal latency, and variable sampling rate, length and update rate. The followed standard formats allow straightforward integration with most of the POD engines. In addition to GNSS orbit, clocks and biases, GMV GSharp® for LEO missions also provides NavBit from GMV’s Global GNSS reference network for radio-occultation missions.
GMV GSharp® for precision agriculture provides PPP-RTK corrections covering all constellations and frequencies with the aim of exploiting the tracking capabilities of high-end user receivers. PPP-RTK corrections are available in the most widely used formats, aiming at maximizing interoperability with different positioning engines’ implementations.
GMV GSharp® for automotive provides safe PPP-RTK corrections, in combination with a safe positioning engine, compliant with the safety standards applicable for automotive, ISO26262 and ISO/PAS 21448 (SOTIF), and the required integrity levels for the target application, up to 10-7/h. The safe positioning engine incorporates techniques and safety monitors that allow to obtain the maximum performance in terms of convergence, accuracy, velocity, heading and safety protection levels.
For more information visit our automotive webpage.
GMV GSharp® for UAVs and robotics combines the provision of PPP-RTK corrections with virtual OSR messages compatible with the RTK positioning engines which are widely used within UAVs and robotics. Additionally, GMV GSharp® positioning engine has been optimised to be lightweight and require minimal HW footprint in terms of computational needs and therefore power consumption.
GMV GSharp® for maritime and offshore maximises the service coverage, by providing together with orbit, clock corrections and biases, global ionospheric corrections for enhanced convergence, without the need of relying on regional or local stations for atmospheric effects modelling. GMV GSharp® for maritime and offshore is delivered via satellite communications for total removal of local constraints.
GMV GSharp® for industrial machinery aims at optimising the end user performances under harsh environments and low dynamics, such as open mining environments with reduced visibility and high multipath. Specificities of each user environment are considered to performed positioning engine configuration tailoring to cope with each customers’ expectations.