GMV’s solution for micro-launcher avionics: another important step towards system qualification
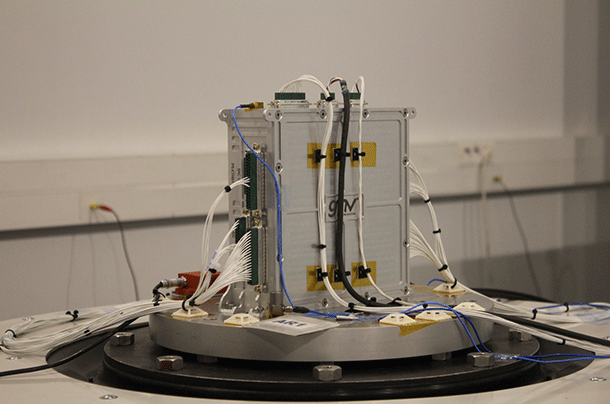
Since 2017 GMV has been working on the design, development and qualification of a complete avionics system for a sounding rocket (MIURA 1 sounding rocket). This avionics encompasses all the vital systems of the avionics system of a classical launcher: the Power subsystem (from energy storage up to power distribution), the Data Handling subsystem (in charge of executing the mission timeline but also collecting data from sensors, actuating valves and sending telemetry), Guidance, Navigation and Control (GNC) subsystem (based on COTS sensors and actuators), Onboard Software, µ-gravity Payload Management and harness. In the frame of this activity GMV is also developing technology for the Autonomous Localization and Termination System.
This design and development of avionics is particularly challenging in such a fiercely competitive market fed by different new-comer candidates or well-known launch services providers that are showing up in the micro launcher world. Other important factors to be borne in mind are the use of commercial elements, and state-of-the-art technologies that can guarantee the required performance quality with an affordable budget.
In addition to the abovementioned factors, two additional characteristics are key elements in this architecture: scalability and modularity. They are the bases for the upscaling of a sounding rocket architecture to a micro- and small-launcher environment.
MIURA 1 data handling systems have been designed with a given reference in mind: namely the classical avionics architectures of European Launchers (ARIANE 5 and VEGA) for the identification of capabilities that such a system needs in order to accomplish its mission. Evolving from the launchers architecture heritage, based on the separation between Telemetry and On Board Processing functions, the architecture has been migrated towards a model more similar to satellites data handling architectures, based on a ‘building block’ named ‘node’.
This approach has resulted in a system whose modularity and scalability are among its strongest characteristics.
The main avionics bus (ring) is the key element of the avionics communication between avionics nodes: the On board Computer (OBC), in the avionics bay; the Engine Control Unit (ECU), in the motor bay; and other nodes in other sections of the launcher. The avionics bus is used to accomplish the launcher mission (command actuators and monitor the propulsion system) but also to collect all the data from all analogue sensors and video cameras and send them to ground via the telemetry transmitter and the antennas.
The avionics system has already passed its detailed design review and is currently in the qualification process, involving functional verification and extensive validation at GMV Avionics Test Bench in Tres Cantos (Madrid) but also environmental qualification tests run at ALTER facilities in Tres Cantos (Madrid).
Considering different hardware configurations of data handling nodes, two qualifications models have been identified whose configuration envelopes cater for different possible hardware configurations: one QM representative of OBC and one QM representative of ECU.
At beginning of September the two qualifications models underwent a complete random vibration campaign in a flight representative set-up. A complete mission was executed during each run of random vibration of the different axes and a preliminary verification of the successful accomplishment of the mission was done in order to give the green light for the execution of the next run.
All interfaces were simulated or stimulated according to a standard mission profile and all data was recorded on-board and on-ground (EGSE). An in-depth analysis of recorded data and EGSE log-files was then carried out, proving full functionality of the two qualification models.
Random vibration tests: details of OBC QM’ test setup
The two qualification models were therefore granted access to the next steps of the environmental campaign: thermal cycling for OBC and thermal vacuum tests for ECU.
Thermal tests have been successfully carried out this week. Also during thermal cycling, detailed functional verification was carried out. During the hot and cold plateau, a complete mission in open loop was executed and a verification of the successful accomplishment of the mission was performed in order to assure the correct continuation of the test.
All interfaces were simulated or stimulated according to a standard mission profile and all data were recorded on-board and on-ground (EGSE). An in-depth analysis of recorded data and EGSE log-files will lead on in the following days to proper reporting, but current outcomes confirmed the full functionality of the two qualification models.
Thermal Vacuum tests: details of ECU QM’ test setup
MIURA 1 is a sounding rocket, developed by PLD Space in Spain, whose mission is to provide a microgravity environment for a payload experiment. MIURA 1 has also another important goal: it will be used as a flying test bed for technologies that will fly with MIURA 5, PLD Space’s micro launcher.
The development of the avionics of MIURA 1 and MIURA 5, carried out by PLD and GMV, kicked off in January 2017; since then the two companies have been working in a technological partnership paradigm, based on proper industrial investments. GMV is in charge of the development and qualification of complete avionics, including not only all vital hardware subsystems of the launchers but also the Guidance Navigation & Control System and the On Board SoftWare System.
ESA has decided to support European private-led micro-launch service ventures in maturation of critical and enabling technologies. In 2018 ESA’s Future Launchers Preparatory Programme placed a contract to co-finance with industry the development and qualification of the Avionics system of the MIURA 1, which can be easily scaled up and re-used for other launchers, including small and micro-launchers. After passing several important design review reviews, the project is now approaching the end of the qualification phase.