Analyzing the impact of Industry 4.0 throughout the value chain
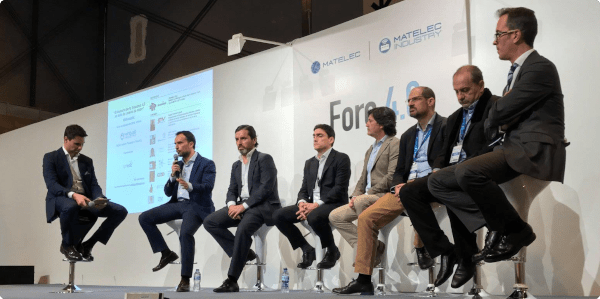
Buying a vehicle nowadays is a very different exercise from a few decades ago. We have now moved on from an almost informationless and optionless consumer to a connected, environmentally-conscious user who is demanding in terms of safety and efficiency. Companies have had to bring their businesses into line with the changing habits and the host of technological changes, bringing the client right into the center of its strategy. This in turn leads to the need to make productive processes more dynamic, versatile and highly modular, to be able to keep up with market trends. This era of digital transformation is ushering in what has come to be called the fourth industrial revolution and it has served as the focus of debate between various experts during Matelec Industry.
Within the Forum 4.0, the Spanish Association of electronic, information-technology, telecommunications and digital-contents firms (Asociación de Empresas de Electrónica, Tecnologías de la Información, Telecomunicaciones y Contenidos Digitales: AMETIC) held a debate on “The impact of Industry 4.0 throughout the value chain”, with the participation of Ángel C. Lázaro, Business Partner of GMV’s Secure e-Solutions sector. The debate addressed all the following themes: industrial assets in the digitalization era; IoT traceability; new business models in connected industry; boosting productivity or saving costs by dint of real-time management and the challenge posed by the demand for professional skillsets.
It is clear that today’s production lines have to adapt to this new situation; this need then impinges on all assets and levels making up these processes. In this digital era, taking in the whole process from sensors and activators to the production management system, we see that sensors in the first place have to send and receive process information to and from a PLC capable of swiftly modifying its control process and, above all, doing so remotely. These devices have to provide much more analyzable information to head off shutdowns or problems. Only a few years ago this was unthinkable. The necessary processing capacity was too high for any programmable controller; nowadays, however, groundbreaking cloud-linked technology like Fog Computing has made this possible.
In line with changes with the production processes, the alteration of a PLC control process has to be much more fleet-footed. For that purpose there are game-changing solutions like VirtualPAC, developed by GMV, which allows PLC-deployed control process to be virtualized so they can be changed dynamically and operated remotely from control centers that may well be located in other countries.
At the level of machines and production phases, collaborative robotics, in combination with artificial vision, is another one of the great advances that permit modularization and adaptability of the production phases. Robots of this type offer great advantages over industrial robots. They can be programmed by their own plant operators; they weigh little and can be easily relocated throughout the factory to carry out other processes. These cobots, run with artificial vision systems, offer the necessary versatility for carrying out highly modular and agile processing tasks that can help us improve product quality, boost productivity, cut production costs and meet the stringent quality standards.
Cybersecurity, the most critical Industry 4.0 factor
One of the stars of this debate was undoubtedly cybersecurity, considered as a necessary technology rather than an option in any digital transformation process. This calls for identification, analysis and management of cyber-risks in industrial facilities, opting for Security/Privacy by design.
IT/OT integration has been with us for some years now. In general this convergence has come about due to the need for operational efficiency and cost reduction. Unfortunately, however, cybersecurity has generally been tagged on afterwards rather than considered throughout. For decades the OT world has been the driver of technological industry due to the dependability, availability, security and robustness demanded for equipment of this type. The trouble is that this technological advance is confronting the OT world with cybersecurity problems that were completely unknown beforehand, and for this very reason we have to transfer everything we’ve learned in IT to OT.
The debate cited examples of how IT cybersecurity is contributing to industrial cybersecurity. From this management point of view, much cyber-risk-management work has now been carried out in cybersecurity that is totally applicable to OT. In terms of technology it is clear that the cloud is coming into its own in OT scenarios and cybersecurity has been working with the cloud for quite some time, so it will also have a contribution to make. Lastly, governmental support is turning out to be crucial for enforcing laws like Spain’s critical-infrastructure-protection law, with its all-in security strategy or the various awareness-raising and skills-training initiatives of Spain’s National Cybersecurity Institute (Instituto Nacional de Ciberseguridad de España: INCIBE).