Machine as a service: an Industry-4.0-enabling business model
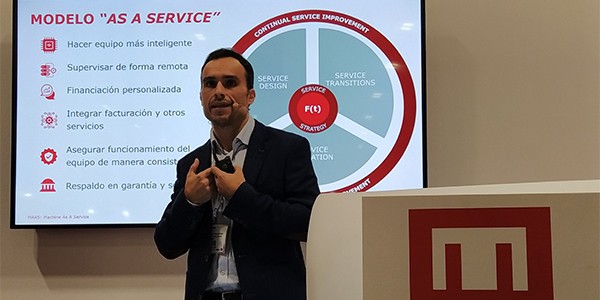
The planet nowadays is being rapidly urbanized. This, together with hyperconnectivity and constant investment in the technological transformation, is steering us towards an increasingly shared and service-based economy. This in turn offers opportunities of outsourcing services, cutting investment costs and getting closer to clients.
Changes that once took years to gel now happen in months, thanks to servitization. “As a service” models aim to help clients adapt to the new environment and transform their systems, focusing on the change from a transactional business to a contractual business. Such a strategy is based on mutual benefit and confidence and, above all, personalization, focusing on end-client services instead of simply supplying a product. These models endow companies with the necessary flexibility for tapping into new technology, eliminating costly updating- and maintenance-outlays. They are also intrinsically scalable, meaning they can be brought into line easily and profitably with changes in the business itself.
GMV has presented this business model, an offshoot of Industry 4.0, at the industrial innovation event called MetalMadrid, talking about use cases and advantages offered by a Machine-as-a-service model in the industrial sector. This chimes in perfectly with industry’s current needs, offering possibilities of personalizing the service and selling a KPI project (timeliness, parts produced, errors detected, etc.) as a standout feature, as well as cutting machine-acquisition-, maintenance and -commissioning costs and risks. This new model provides industry with smarter resources capable of supervising remotely and personalizing funding and other services, while also ensuring the equipment works properly with warranty and safety backup. This business model can also be rounded out with the use of applications controlling all assets in a safe, secure and centralized way.
As examples of the application of this business model we now coexist with inspection systems based on autonomous mobile platforms using modular sensor kits where billing is based on information provided and distances run. Similarly, artificial-vision applications based on neural nets and reinforced learning are capable of carrying out classification tasks by learning from human knowledge, with billing based on classified images. Other features of this model are collaborative and industrial robotics, focusing on the output-boosting automation of production lines with low implementation-, programming- and plant-distribution costs. In this case, as the manufacturer is present throughout the whole robot’s life and not only up to plant implementation, equipment-use data can be obtained and monitored to bring the supply progressively into line with real client needs.