Operational and Predictive Maintenance to Streamline the Industry
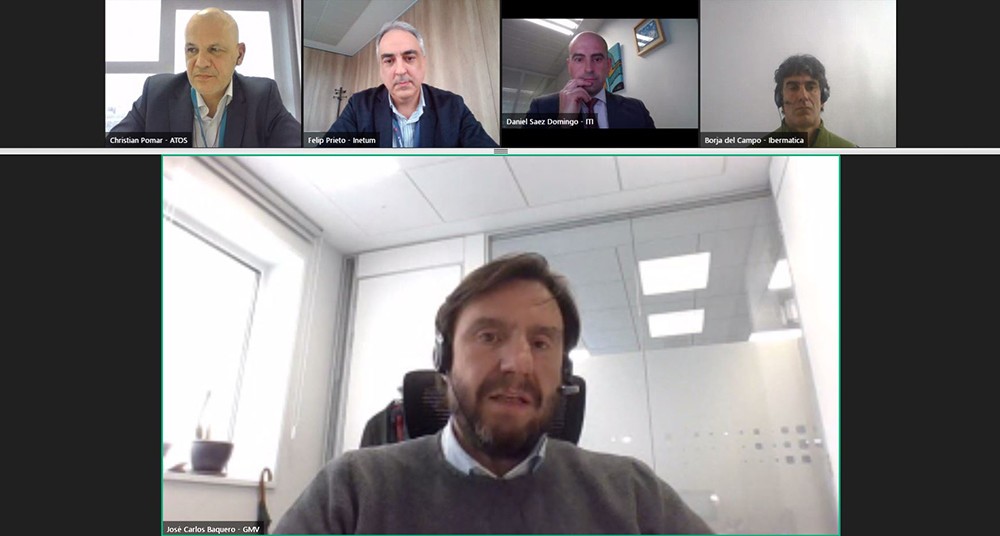
Implementing innovative solutions, where process digitalization plays an essential role, is key to reducing operating and production costs, reaching sustainability goals, and consolidating the transformation to Industry 5.0. Along this line, applying disruptive technologies to simulate critical operations, such as maintenance, is key to optimizing processes, resources, and energy. The needs of consumers are also changing at an ever-greater pace, forcing companies to adapt and anticipate in their actions. This is where Artificial Intelligence can provide a great deal of value to these types of industries, increasing their production capacities and improving their efficiency.
In the industrial realm, predictive models cover a series of statistical data mining techniques, predictive modeling and machine learning that can use data to analyze trends and, without being induced, find repetitive patterns on its own that help companies anticipate scenarios and make decisions such as risk assessment, anomaly detection in manufacturing or specific operations of any type.
Industries with processes that use connected devices and sensors need to know how the plant will behave outside of normal parameters to make decisions on optimizing it. However, the cost and risk of configuring the plant for that behavior is very high, which is where digital twins come into play. This technology is fed with real-time data that is extracted from all the physical assets involved in the production process, because they are all digitalized, stored and processed, and interact with other virtual data and data from interactions among themselves. This specific information is based on the record of data from real usage cases, so it is a great tool for analyzing and understanding the different product phases, making it possible to improve them. “To improve the maintenance processes, there is a change in the strategy of installing sensors and storing the data they produce. It is a strategy based on usage cases; that is, selecting an industrial process (or part of it), defining the objective and looking at how to improve it by incorporating these innovative technologies,” says José Carlos Baquero, Director of GMV’s Artificial Intelligence and Big Data Division, during a roundtable meeting on “Industrial Process Digitalization and Simulation,” organized by enerTIC at the “Foro Tendencias 2022: Next Industry 5.0” event.
At GMV, we are working with this type of technology in anomaly detection, indicating where the problem is occurring, in automatic quality inspection tasks with artificial vision techniques, in warehouse automation with autonomous robotics, in collaborative robotics in labs, or in the design of digital twins to better understand the behavior of a plant and to train machine learning models.